Case Study 03
Lean Store/VLM SAP Integration for FIFO Management in Warehouse Automation
Overview
A global manufacturing company specializing in high-precision automotive components. The company operates multiple warehouses that support Just-In-Time (JIT) production to keep the assembly lines running efficiently. However, maintaining FIFO, tracking physical stock, and ensuring inventory accuracy in a timely manner have been persistent challenges.
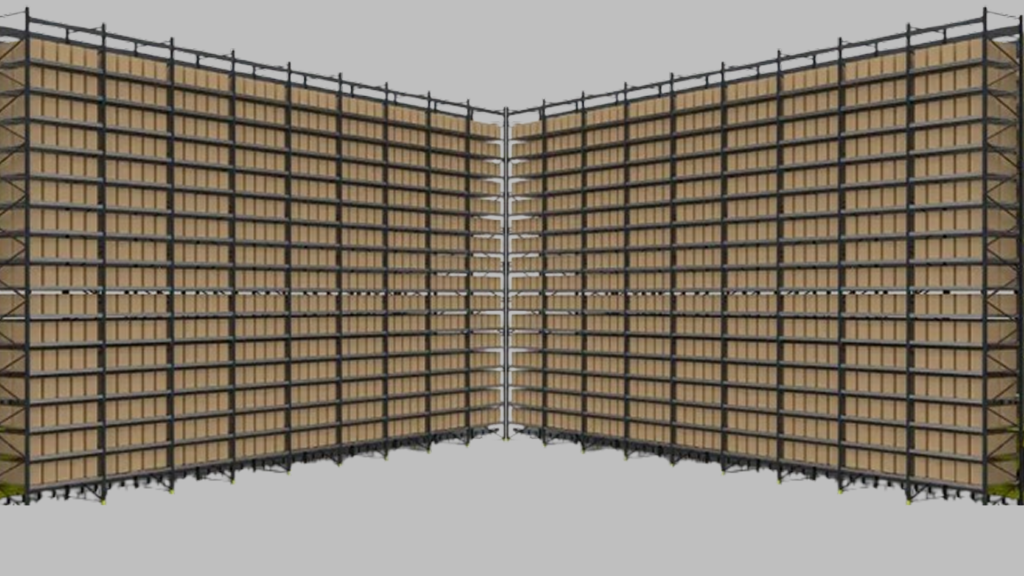
Problem Statement
- FIFO Compliance :Manual tracking often led to incorrect stock rotation, resulting in expired parts being used and production delays.
- Daily Physical Stock Counting: Operators spent significant time manually reconciling physical stock with system data.
- Space Constraints: Traditional storage methods resulted in inefficient space usage and frequent manual picking errors.
- SAP Integration: Lack of real-time synchronization with SAP led to stock mismatches between the system and warehouse floor.
- Labor Costs: High reliance on manual effort increased operational costs.
Objectives
- Automate inventory management through Lean Store/VLM (Vertical Lift Module) or Vertical Carousel systems.
- Integrate with SAP for real-time stock updates.
- Enforce FIFO to avoid expired or obsolete stock being used in production.
- Eliminate manual stock counting and reduce discrepancies.
- Maximize storage efficiency through vertical automation.
- Enhance production planning with real-time and accurate inventory data.
- Enable user-wise access controls, track operator/machine performance, and automate error handling.
Solution: Lean Store/VLM & Vertical Carousel Integration with SAP
Key Features and Software Highlights
Vertical Lift Module (VLM) / Vertical Carousel
- Compact, automated systems store and retrieve parts vertically, maximizing space.
- Faster retrieval reduces walking time and improves operational efficiency.
- FIFO logic ensures older stock is picked first automatically.
SAP Integration
- Real-Time Data Sync: Stock levels, receipts, and retrievals are updated instantly in SAP.
- Material Management Updates: SAP reflects the most accurate stock positions after each operation.
- Auto Stock Adjustments: System updates SAP after every transaction without manual intervention.
FIFO and Batch Tracking
- Items are stored with associated batch numbers and timestamps.
- Automated logic ensures the oldest part is always retrieved first.
- Expired stock usage is fully prevented.
Physical Stock Calculation
- VLM-integrated sensors and barcode/RFID tracking continuously monitor actual inventory.
- Eliminates need for daily physical checks — system stock is always in sync with real stock.
Andon System for Monitoring
- Large displays provide real-time visibility of:
- Stock levels
- FIFO status
- Retrieval progress
- Machine availability
Advanced Operational Features
User-Wise Access Control:
- Role-based access ensures different permission levels (operator, supervisor, admin).
- Activity logs are maintained per user.
Weight Management:
- Real-time weight checks during inbound/outbound ensure correct item quantity.
- Prevents mismatch errors and unauthorized retrievals.
Machine Error Handling:
- All system faults are logged with timestamps and error codes.
- Auto-notifications sent to maintenance or supervisors.
- Downtime tracking available for root cause analysis.
Performance Monitoring:
- Operator Efficiency: Tracks items picked/stored, error rates, and speed.
- Machine KPIs: Measures tray access time, retrieval speed, and uptime/downtime reports.
- Enables continuous improvement using performance analytics.
Workflow Overview
Inbound (Automated Storage)
- Items scanned at entry using barcode/RFID.
- VLM auto-assigns optimal slot based on FIFO logic and part type.
- Stock location and timestamp updated in SAP instantly.
Storage & Inventory Management
- Based on JIT requests from SAP, VLM retrieves items in FIFO order.
- Live updates pushed to SAP after every movement.
- No manual intervention or confirmation needed.
Physical Stock Calculation
- VLM sensors + RFID/barcode integration provides precise live stock visibility.
- Continuous background sync with SAP.
- No need for cycle counting by floor staff.
Outbound (Production Supply)
- SAP triggers JIT call for required items.
- VLM retrieves correct batch in FIFO order.
- Delivered directly to production with quantity and batch auto-logged.
Benefits
- Real-Time Inventory Sync with SAP: Eliminates data mismatches.
- Efficient FIFO Handling: No manual sorting required—100% automatic.
- Space Optimization: Utilizes vertical space to double storage capacity.
- Labor Savings: Automation reduces manual intervention drastically.
- Operator/Machine Performance Insights: Enables accountability and productivity tracking.
- Reduced Errors: Real-time checks on weight, movement, and location eliminate picking mistakes.
- Machine Health Monitoring: Error history and recovery logs ensure long-term system stability.
Lessons Learned
- SAP ↔ VLM Communication Must Be Real-Time: Lag causes discrepancies.
- High-Demand Parts Should Be Prioritized in Retrieval Paths.
- User Access Rights Should Be Configurable and Audited.